Collyhurst Village - DEX Construction
Collyhurst Village is part of the Victoria North regeneration masterplan, the largest renewal project ever undertaken in Manchester.
The Strategic Regeneration Framework (SRF) plan promotes a commitment to putting environmental sustainability at the heart of the project and is being delivered in stages over the next 15-20 years. To create 15,000 sustainable new homes, improve transport links, community facilities, and green spaces, with the creation of a new City River Park.
The joint venture partners Manchester City Council and Far East Consortium (FEC) a global property conglomerate are working together on the first phase of Collyhurst Village to build 244 energy-efficient new homes, a shop, community space and new park on cleared land adjacent to Rochdale Road. The housing development designed by Buttress Architects is a mix of townhouses and apartments and will be built by Far East Consortium’s in-house contractor DEX Construction.
To create a sustainable neighbourhood for current and future generations, 100 of the new homes will be Council-owned properties available for social rent, with the remainder for private sale. Key features include dedicated bike storage spaces for residents as well as parking spaces which are enabled for electric vehicle charging.
The development of the new park will require the demolition of 29 existing properties. The new homes will be built before demolition happens so residents can move straight into a new home and not have to move out of the area.
Project Summary
To support primary contractor DEX Construction with delivering the Collyhurst village scheme that forms part of the Victoria North regeneration masterplan. We firstly erected a scaffold around the sample pod near the on-site offices before moving onto the main site area and erecting a series of HAKI system scaffold configurations up to 5-lifts. To assist with constructing a mixture of townhouses, apartments, and retail space to improve local services and help transform the neighbourhood. This development phase includes more than £35m of public investment and represents the first large-scale regeneration in Collyhurst for over 50 years.
With a national shortage of new homes available based on current demands, the government has encouraged the adoption of ‘modern methods of construction’ (MMC). The new homes within the development incorporate modern building techniques utilising timber frame kit construction so sections can be pre-made in off-site workshops prior to assembly on-site for greater efficiency. This innovative approach helps to ensure the programme remains on schedule by building the new homes more quickly. Timber frame construction is also deemed more environmentally-friendly than traditional ‘brick-and-block’ masonry housing and now accounts for many newly constructed social housing developments throughout the UK.
HAKI modular system scaffolding is well suited to support this change and ideal for fast-paced new build construction projects. It can increase productivity on-site by up to 60% due to the unique quick, simple ‘hook-on’ method of erection when compared to traditional tube and fitting still widely used in housebuilding. Usually, tube and fitting is progressively erected one lift at a time to support bricklayers and other trades.
Additionally, to support the newbuild construction and fit-out phases, installed HAKI Staircases help to improve efficiency on-site and give scheduled tradespeople, including phase bricklayers and glaziers, safe access/egress to all levels whilst HAKI loading bays enable the safe and efficient delivery of materials and waste removal.
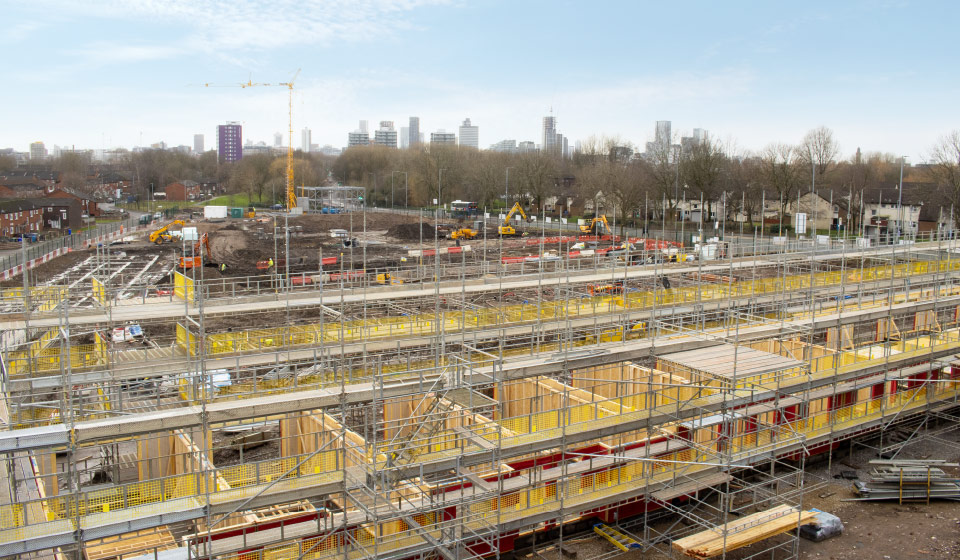
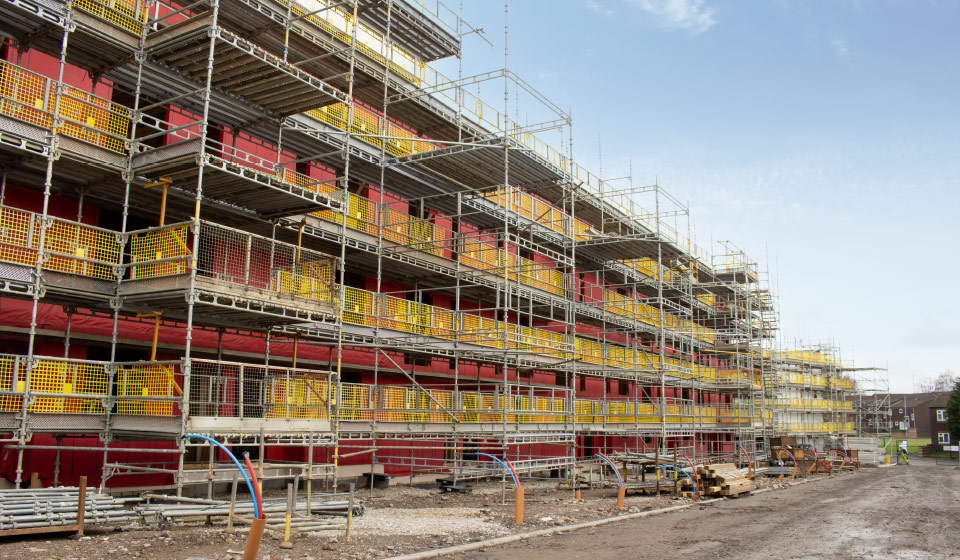
Value Engineering
It soon became apparent that meeting the completion date would be challenging after the primary contractor incurred unforeseen delays while finishing the groundworks. So, to overcome this initial setback, Enigma’s Operational Team worked closely with DEX representatives on-site to create a revised planning schedule that enabled the project programme to commence swiftly. After erecting a sample scaffold, it was possible to identify potential coordination and sequencing issues while collaboratively working with all sub-contractors operating on-site. This process helped to resolve any potential problems before the commencement of the permanent works that could cause setbacks going forward.
We also continued to proactively liaise with all sub-contractors working on-site to ensure any potential concerns were dealt with promptly to avoid unnecessary delays that could prevent the works from progressing.
Health and safety are paramount at Enigma, and all scaffold erection, adjustments, and dismantling duties were carried out safely.
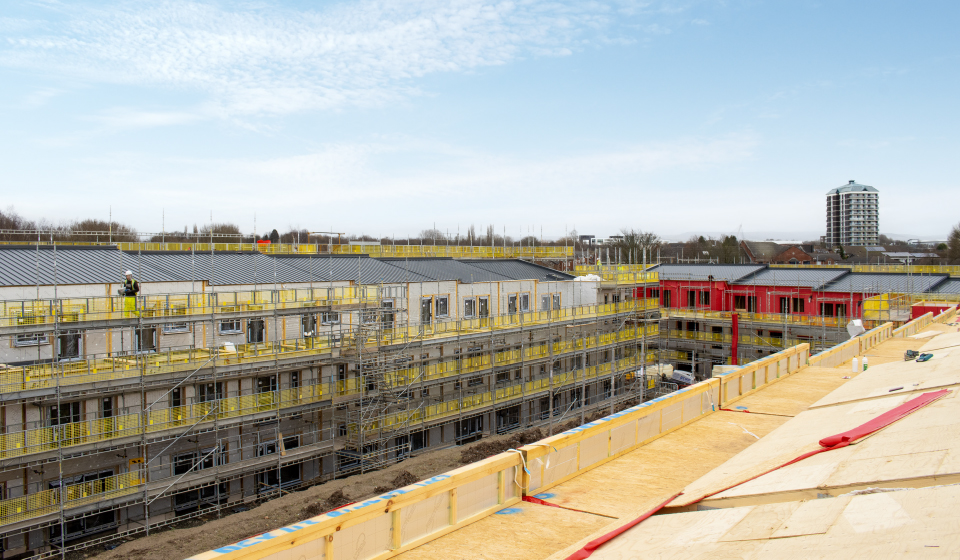
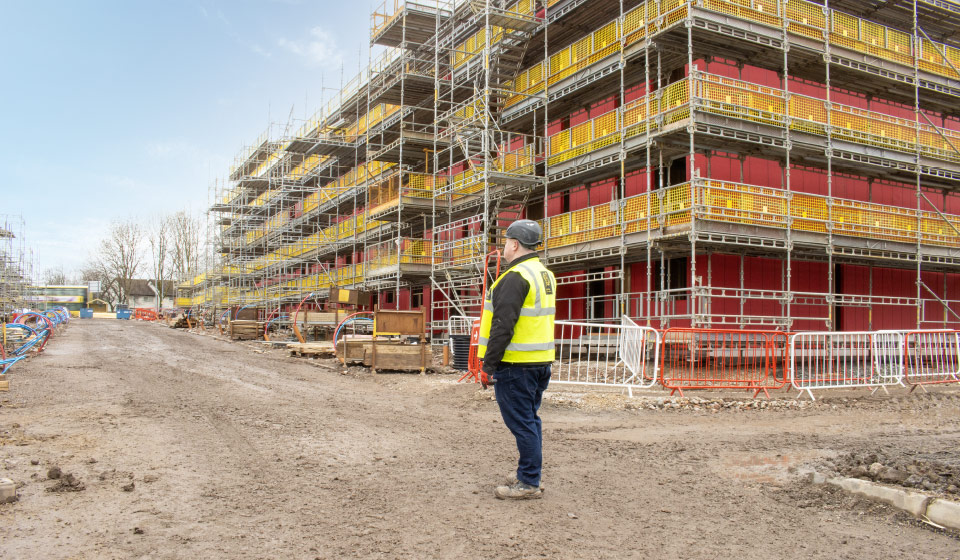