Princess Quarter
Provision of temporary access and extensive structural propping solutions to redevelop a disused 1950s concrete frame building into retail units and modern office accommodation.
Morganstone is the appointed primary contractor by Kartay Holdings Ltd to redevelop the existing building constructed in the 1950s. The disused end terrace, concrete frame construction four-storey building has been vacant for over 7-years and revitalised to regenerate the heart of Swansea city centre and create a sustainable neighbourhood.
The contemporary development comprises ground floor retail units with the upper three floors utilised for modern office accommodation. The project phases include the conversion, external refurbishment (including glazed curtain walling installation) and building of a two-storey extension comprising a roof terrace, three rooftop meeting pods and green infrastructure.
The new building utilises low carbon technologies in the form of high-efficiency air source heat pumps providing heating and cooling via a variable refrigerant flow (VRF) system, designed to be ‘all-electric’ to negate the reliance on fossil-fuel, lowering the buildings longer term carbon footprint.
Project Summary
Morganstone appointed Enigma to provide access solutions and propping support arrangements to aid the safe demolition of designated areas within the existing building before sections of the erected scaffold were adapted to enable access for the new construction and façade installation phase.
Two site visits were carried out by Enigma engineers to assess the site before works commenced and then finally to survey the scaffolds once built. A total of four bespoke designs with supporting calculations have been provided by Enigma, with all design’s undergoing multiple revisions to ensure every detail is covered.
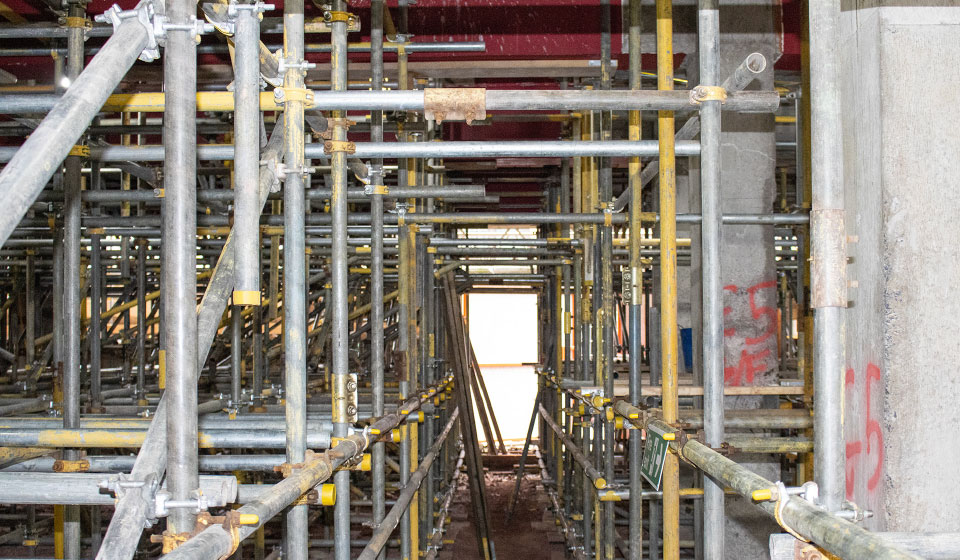
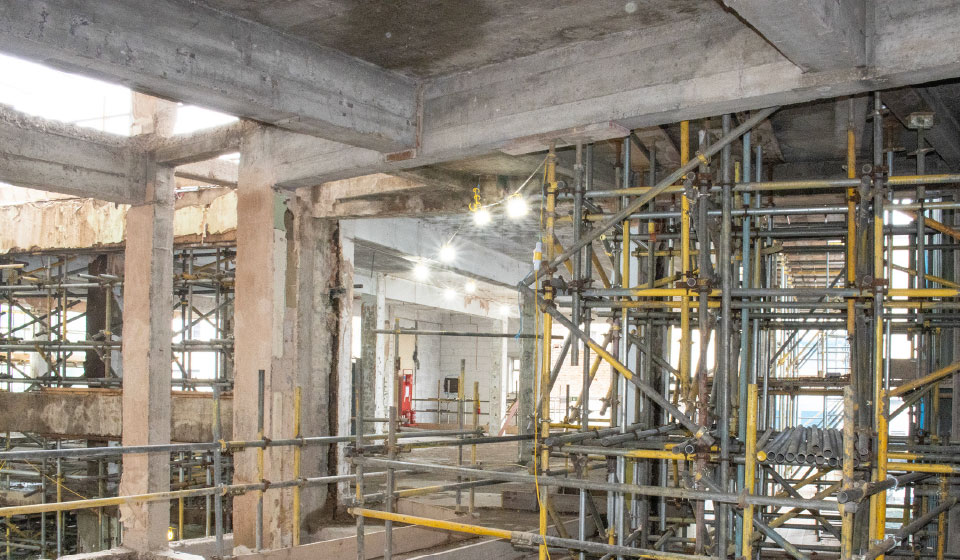
Value Engineering
Phased demolition and construction scaffold
A phased scaffold was required on Princess Way and St Mary’s Street to aid the partial demolition of the existing building before being adapted to assist the construction and new façade installation. To keep the changes between phases minimal, Enigma engineers and operatives working onsite consulted with Morganstone representatives to discuss building offsets and space limitations. The scaffold configuration design for the demolition phase was then revised so that the outer scaffold upright would become the inner upright for the construction and façade installation phase. This solution was also more sustainable as it significantly reduced erection and dismantle times and the amount of scaffold material delivered to site.
Propping Works
After a structural engineer conducted a preliminary site visit, it highlighted the need for extensive propping to aid the demolition works by helping to stabilise the building and provide structural support.
Based on the engineer’s report findings, Enigma’s Design team overcame the challenge and provided an initial design proposal within a few days. The proposed solution was then further adapted after liaising with the client and on-site team about their specific requirements and site constraints. This demonstrates our ability to respond quickly to project changes and efficiently provide a revised solution without compromising quality.
The structural engineer’s report identified high reaction loads of up to 1200 kN in places throughout the building. So Enigma transferred the loads from the top floor down to the foundations by erecting a bespoke birdcage propping scaffold. Also, to ensure the scaffolding could safely withstand the exerted loads, the biggest axial loadings were calculated and checked against the allowable loads of the scaffold uprights.
Careful consideration and planning were needed to spread the axial loads via sole board details. Notional horizontal loads were calculated against bracing patterns and jacking details to ensure the overall structural integrity of the scaffold. Also, all the mentioned solutions above were clearly illustrated in standard details included on the design to provide Enigma operatives erecting the scaffold on-site with safe tolerances.
Later in the project timeline, the suitability of the permanent structures’ floor slabs to support the additional mechanical loadings from the required plant and machinery was in doubt. So Enigma engineers evaluated the potential problem by calculating the most excessive loads exerted throughout areas of the building. Based on the study data, the propping designs were updated to ensure the continued structural integrity of the scaffold structure and the encompassing concrete frame.
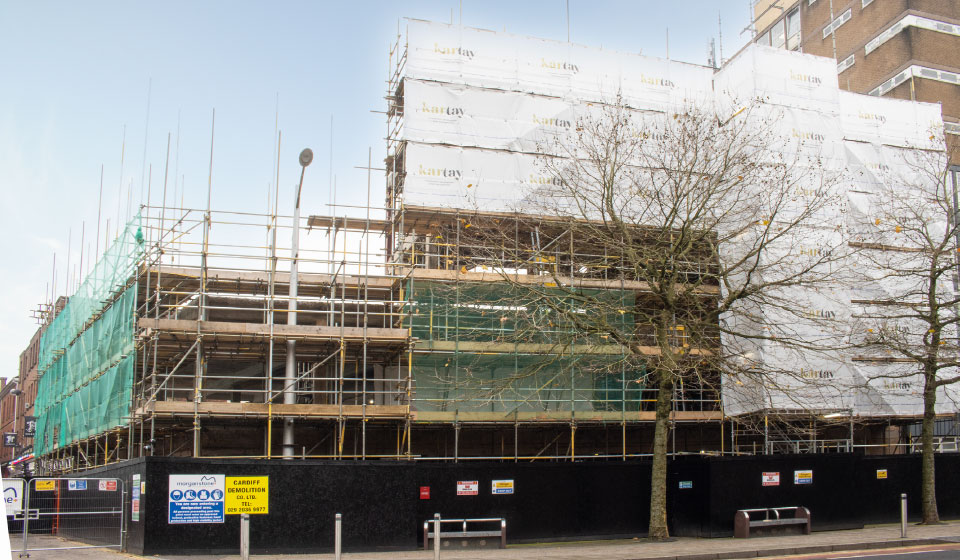
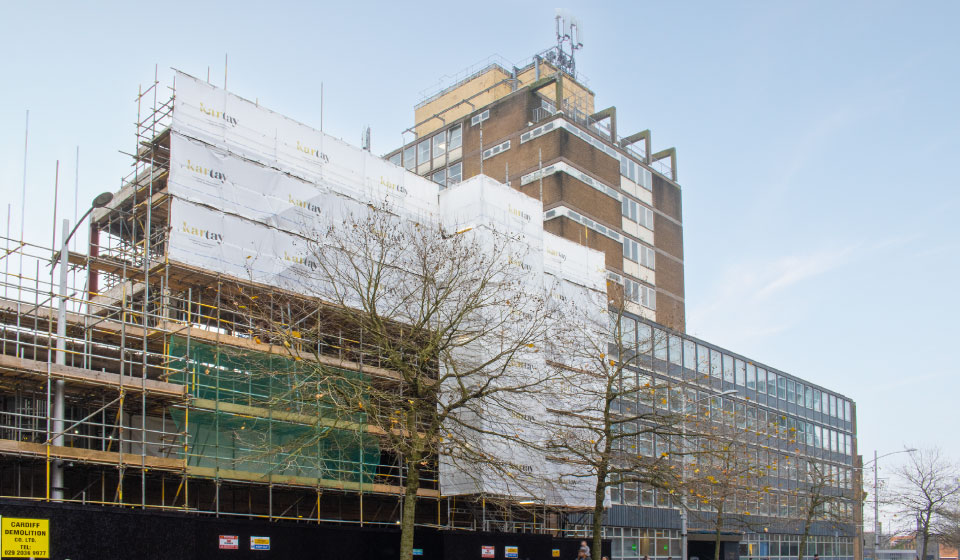